Hallo Foristi,
Sutschemang (pöh a pöh) geht es weiter mit der Arbeit am Fischkai von Geesthaven. Nachdem nun auch die letzten notwendigen grobmotorischen Arbeiten an den Modulkästen erledigt sind (Anbringen massiver 35 x 35 mm „Balken“ an der unteren Verderseite des Modulkastens um eine „Auflage“ für die Wasseroberfläche zu bekommen, an die später Bretter für die Fischdampfer angeschraubt werden können), kann es mit dem finalen Verkleben der Gebäude auf dem Untergrund weitergehen. Da ich die Grobmotorik lieber draußen erledige, war angesichts des bis vor kurzem dauerndem Winterwetter Feinarbeit drinnen angesagt.
Die Holzkonstruktionen der Fischhalle habe ich ja bereits im Teil 2 vorgestellt, jetzt habe ich mich mit den notwendigen Rolltoren beschäftigt und die „Steingebäude“ behandelt.
Die Rolltore
Meine Fischauktionshalle weist außer den Oberlichtern keine Fenster auf, Statt derer gibt es zahlreiche, fast raumhohe Rolltore, die im geöffneten Zustand genügend Licht in die Halle fallen lassen. Auch die elektrische Beleuchtung war in der von mir präferierten Zeit schon erfunden (die wird von mir aber aus „Modellbahnfilosofischen“ Gründen nicht dargestellt). Die Hallentore standen meist offen um den Wind durch die Halle wehen zu lassen; Fischreste neigen schnell zum Ausbilden des typischen „Gammelgeruchs“, der die olfaktorische Szenerie eines Fischereihafens eindrucksvoll bestimmt. (Mal sehen, vielleicht bringe ich unter dem Modul eine Aufnahme für teilentleerte Fischkonservendosen an ;-)). Auch die Tnf-Kühlwagen standen zwischen ihre Einsätzen mit geöffneten Türen in den Abstellgleisen.
Nach meinen internen Recherchen brauche ich ca 90 Torflügel. Da ich meine Ausdauer kenne, habe ich nicht selbst Hand an eine Messerklinge gelegt sondern einen neumodichen Laserstrahl die Arbeit verrichten lassen. Schnell und präzise „stichelt“ er die benötigten Einzelteile aus Karton aus; immerhin waren drei eng belegte DIN A4 Bögen notwendig.
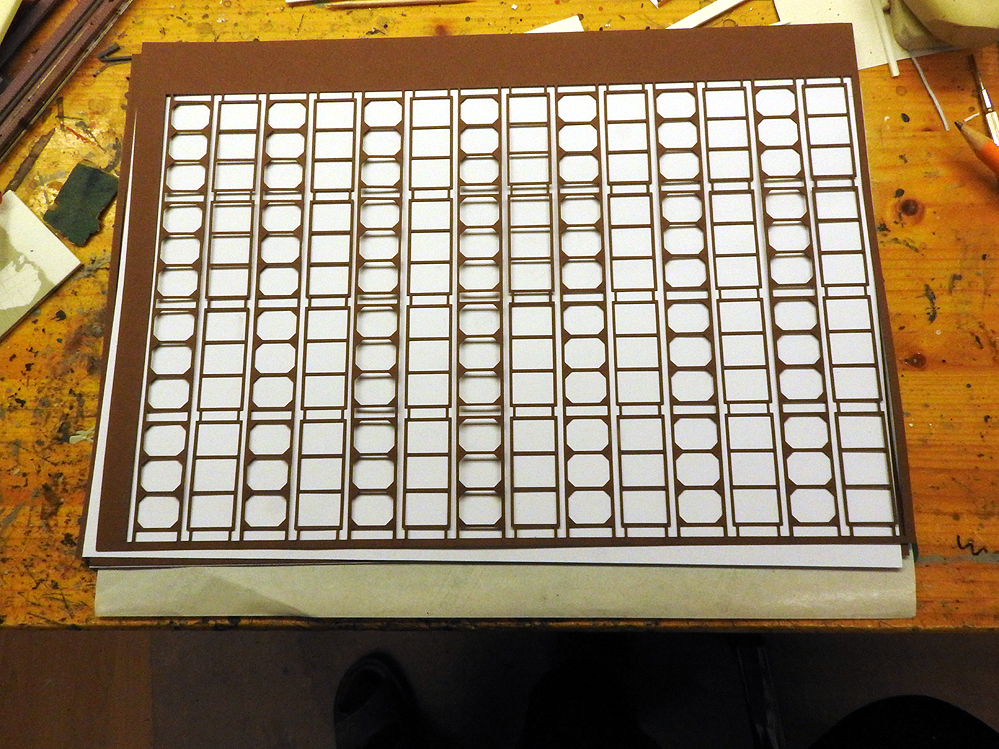
Die Einzelteile auf 300 gr Tonkarton
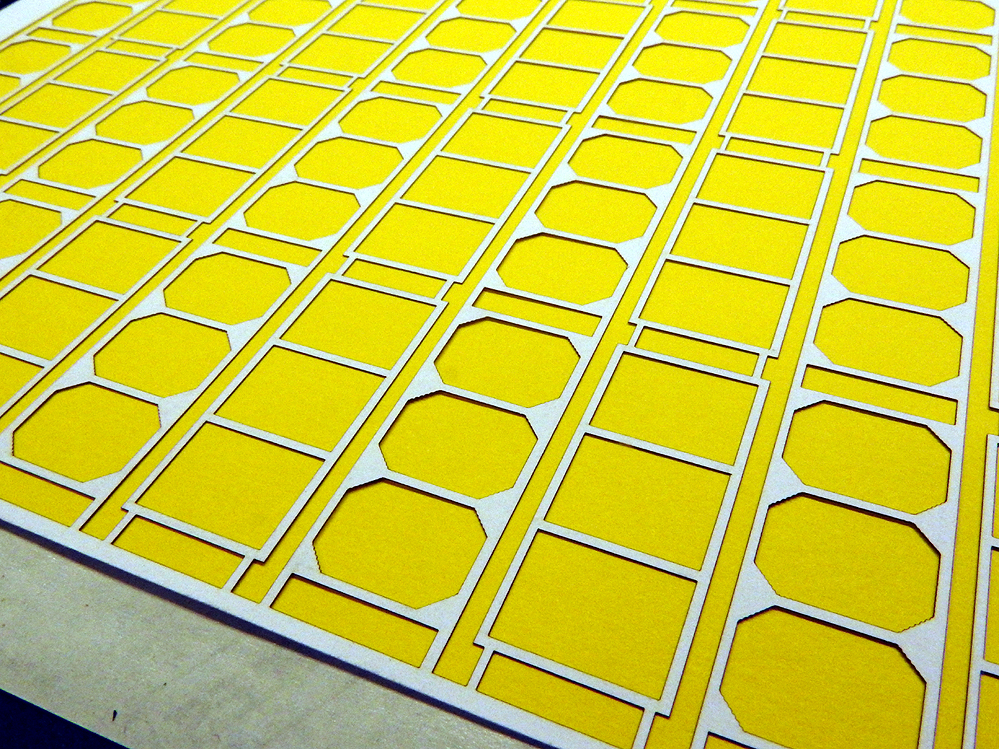
Die Einzelteile auf 160 gr Papier/Karton
Natürlich ist erst einmal zu erkunden, welches Material sich am besten für die Nachbildung der Tore eignet. Hier geht es im Wesentlich um die Materialstärken damit das Ganze nicht zu „klobig“ wird. Getestet habe ich einen 330 gr Tonkarton, 0,4 mm dick und ein 160 gr Papier/Karton, 0,2 mm dick.
Hier mal die Probe-Ergebnisse:
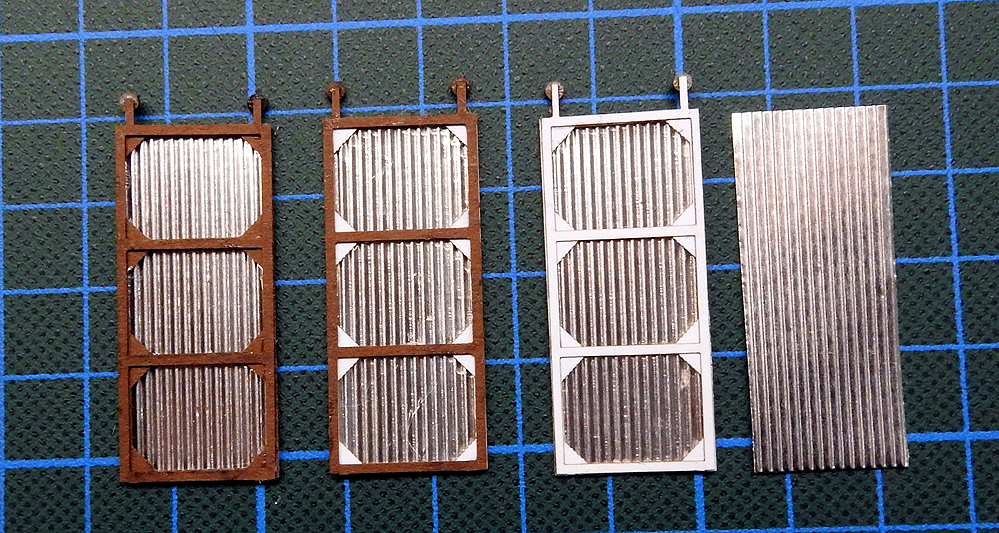
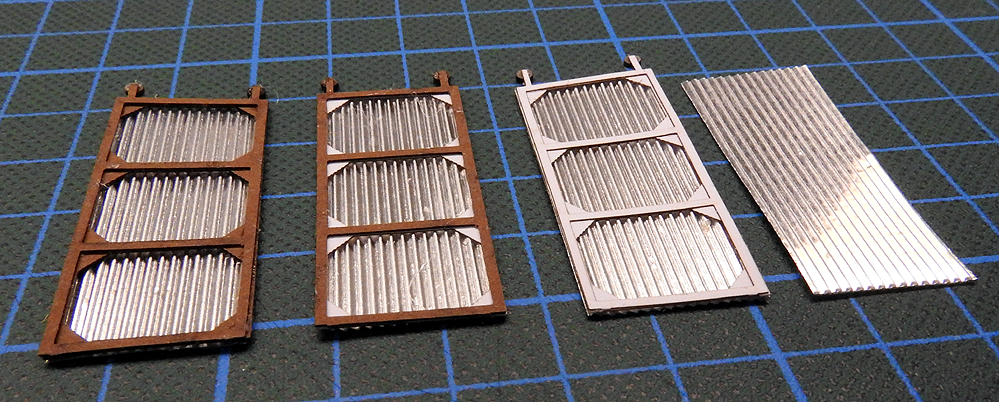
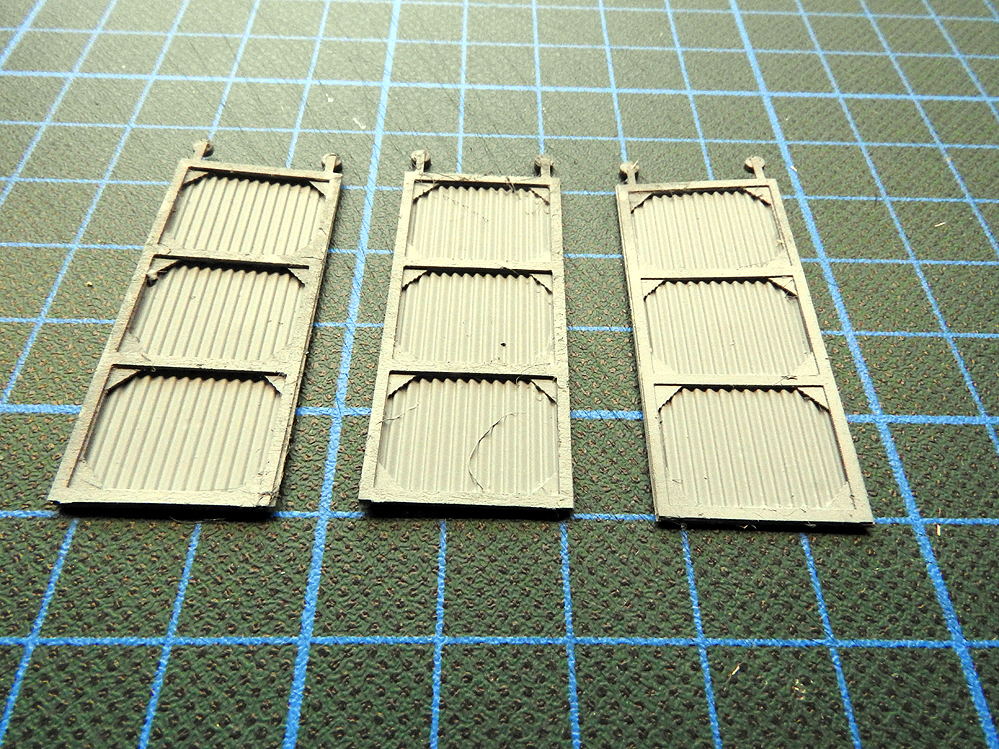
So sieht dann der erste Probeanstrich mit dem Pinsel aus
Ich habe mich für die Rahmenkonstruktion aus komplett dünnem 160 gr Material entschieden, Die Torfüllung besteht aus einer Wellaluminiumplatte mit einer 1 mm-Welle (Gibt es im Architekturbedarf von Schulcz) Aluminium ist mit dem zur Verfügung stehenden Laser leider nicht zu schneiden, aber hier tat es auch mein Olfa-Messer mit seinen Abbrechklingen. Wider Erwarten lies sich die Wellplatte leicht schneiden ohne dass etwa „die Welle“ an den Schnittkanten plattgedrückt wird.
Ach ja, eine mehr als notwendige Anzahl von 2 mm „Rollen“ produzierte der Laser binnen weniger Minuten. Da brauche ich nicht meine Nachbarschaft mit einem Locheisen zu nerven.
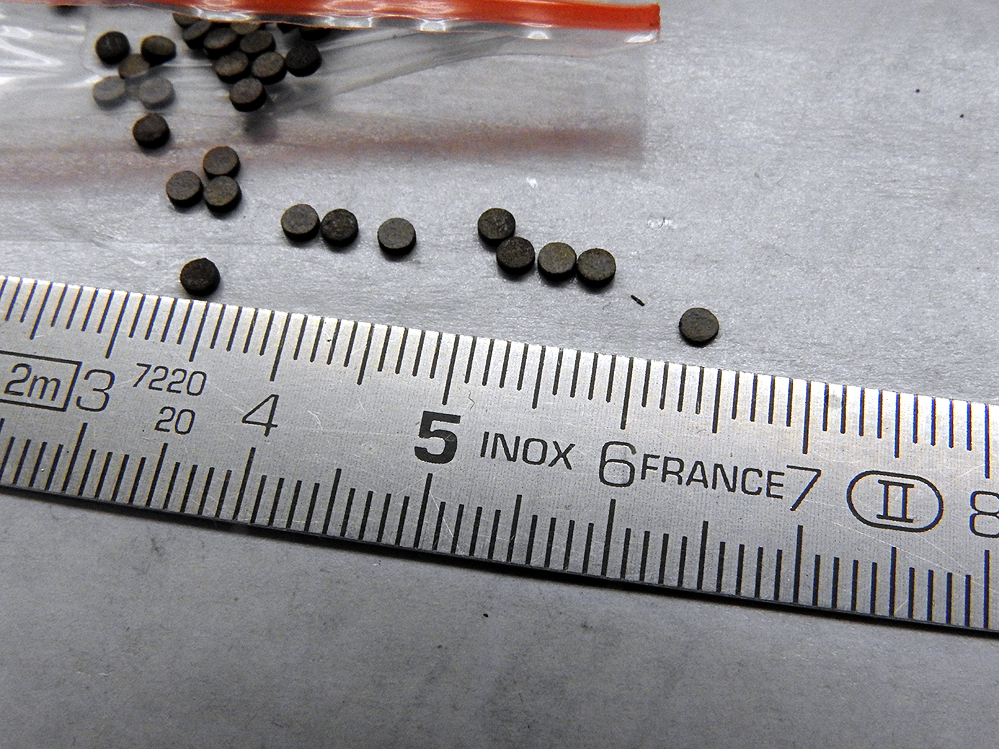
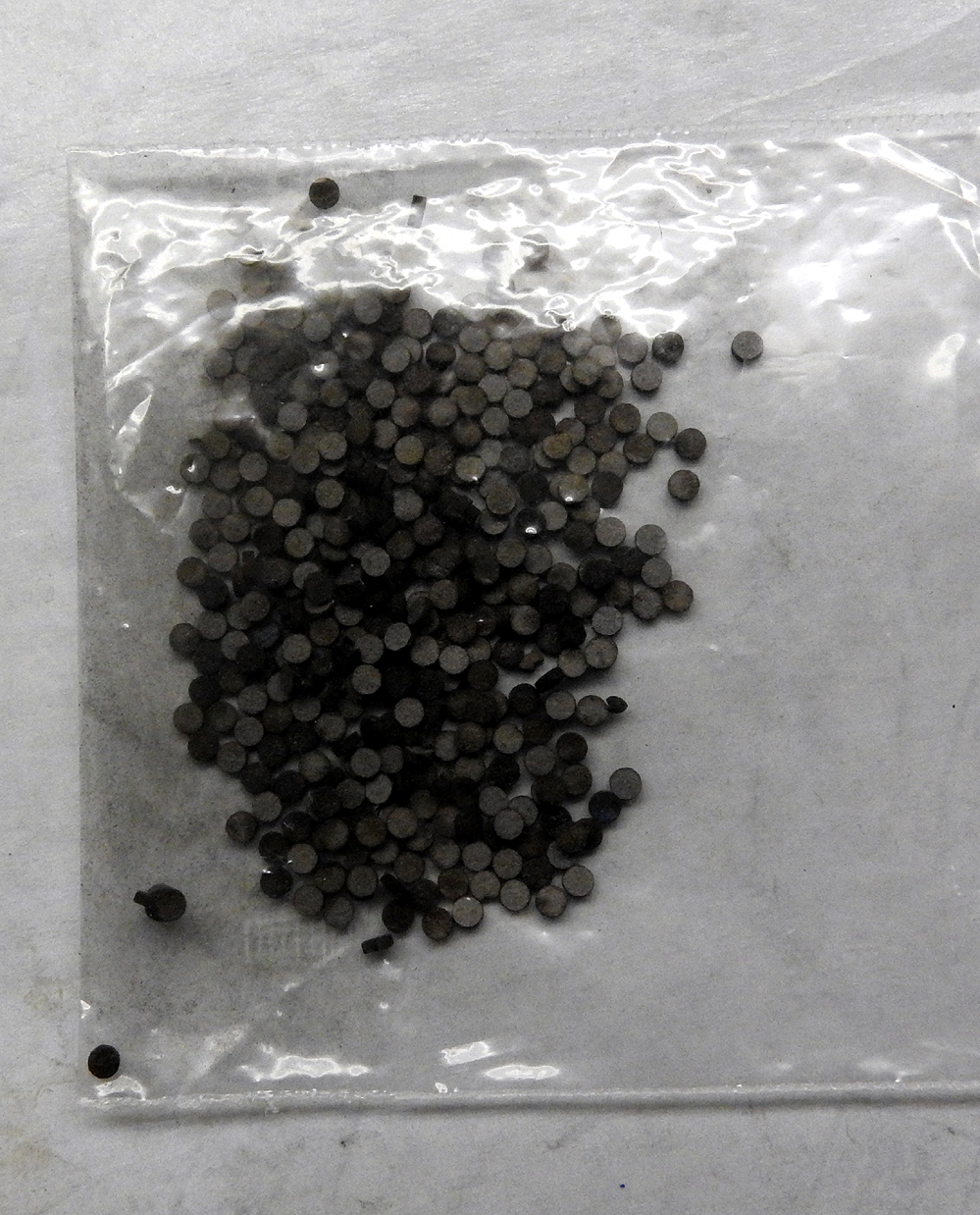
Nach der Vereingung der Bauteile zu fertigen Toren habe ich sie mit einem Grau von Revell-gespritzt. Der Farbton ist der gleiche wie bei der gesamten Hallenkonstruktion, die Gesellschaft ist halt sparsam und es müssen nicht viele verschiedene Töpfe beschafft werden.
Bei der „Alterung“ macht sich das natürlich bemerkbar: Holz rostet bekanntlich nicht und so bekommen die Holzwände halt nur einen Hauch von „a darker shade of pale“, während die Eisenkonstruktion der Tore mit Rostfarbtönen ins Auge stechen können. Ich werde in den nächsten Tagen alle Tore farblich misshandeln und nach dem Trocknen je nach ihrem Verwitterungsgrad klassifizieren um passende Päärchen zueinander zu bringen.
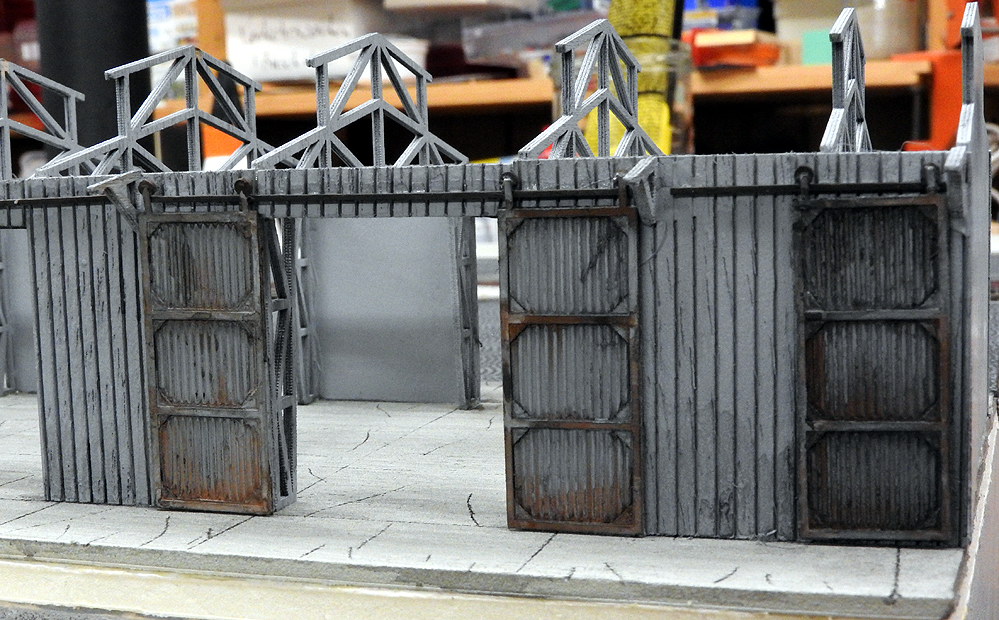
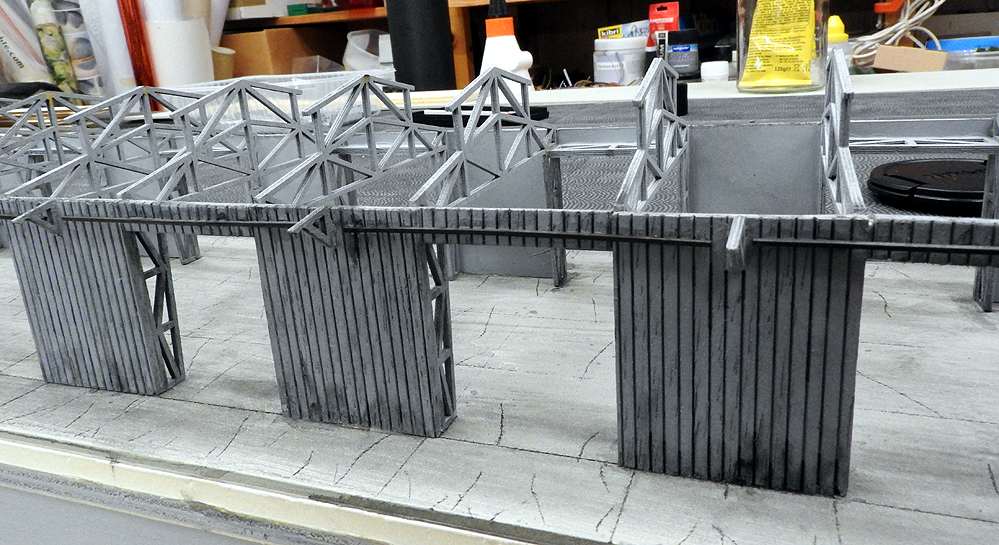
Die mittlerweilen grau gespritzten Hallenteile habe ich auf die „noualliermäßig“ behandelte Kapaplatte mit Pattex aufgeklebt. Für den korrekten Abstand habe ich mir aus 3 mm Finnpappe entsprechende Abstandshalter gefertigt. Sie garantieren, dass die „Stürze“ auch sicher passen.
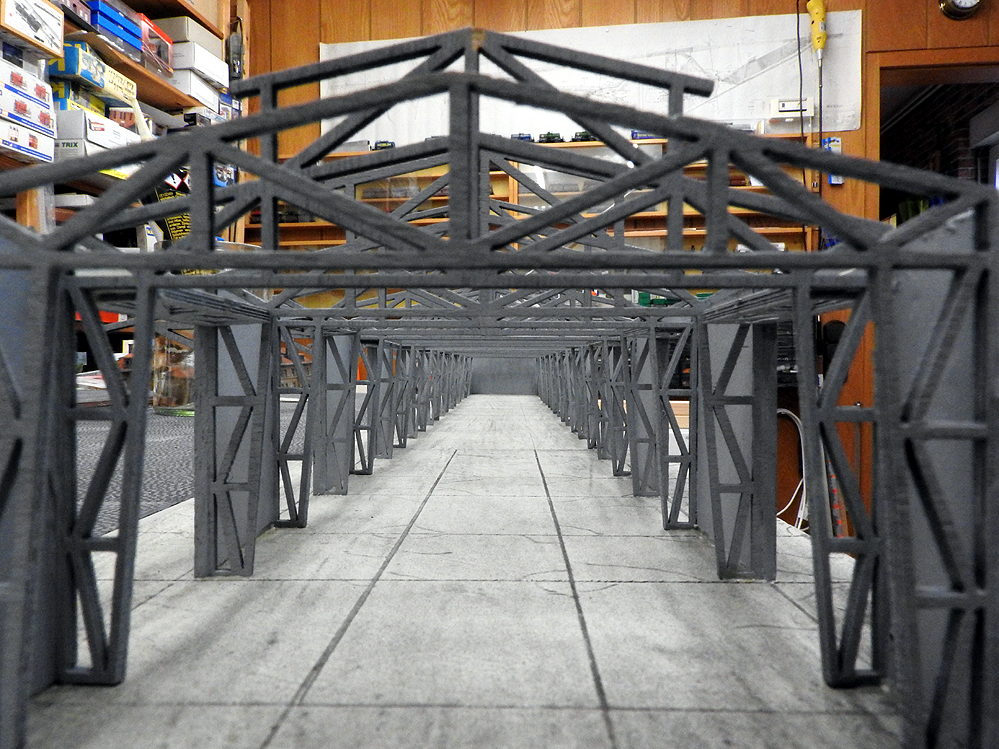
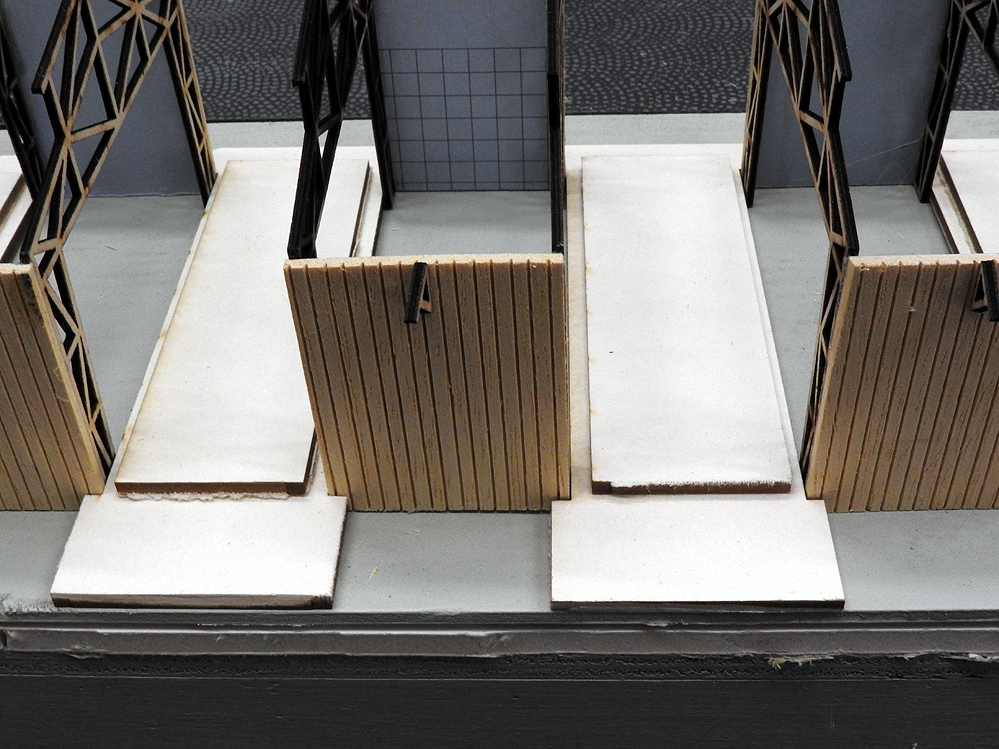
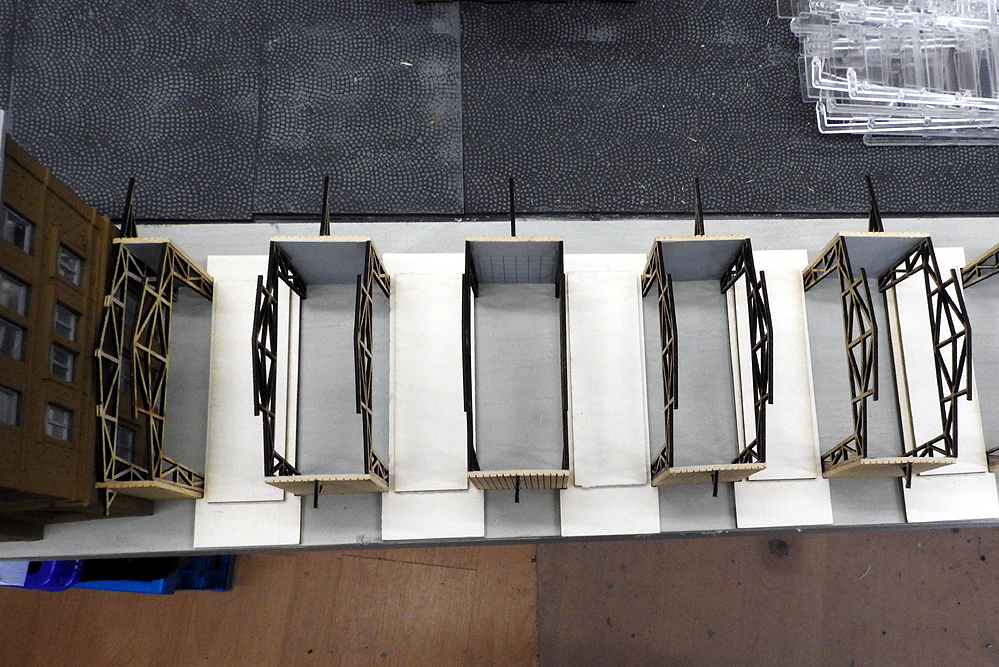
So wird auch der Abstand zur Kaikante immer gleich
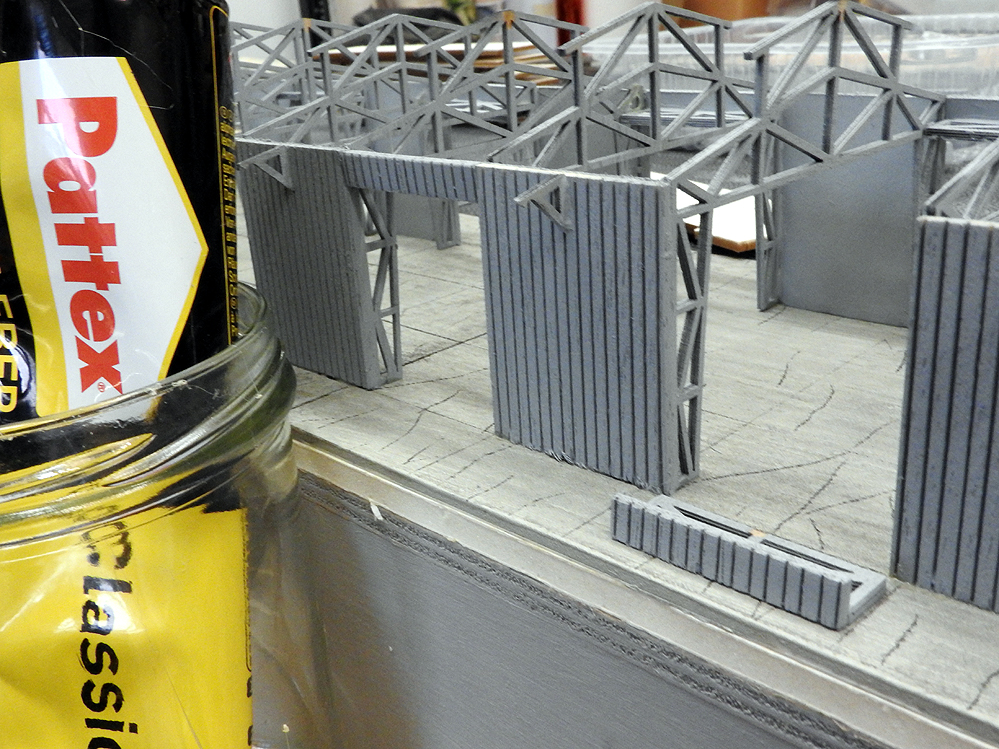
Die "Stürze" sind zur Stabilisierung hinten mit einer Fachwerkkonstruktion versteift und werden mit Pattex an ihre Plätze geklebt.
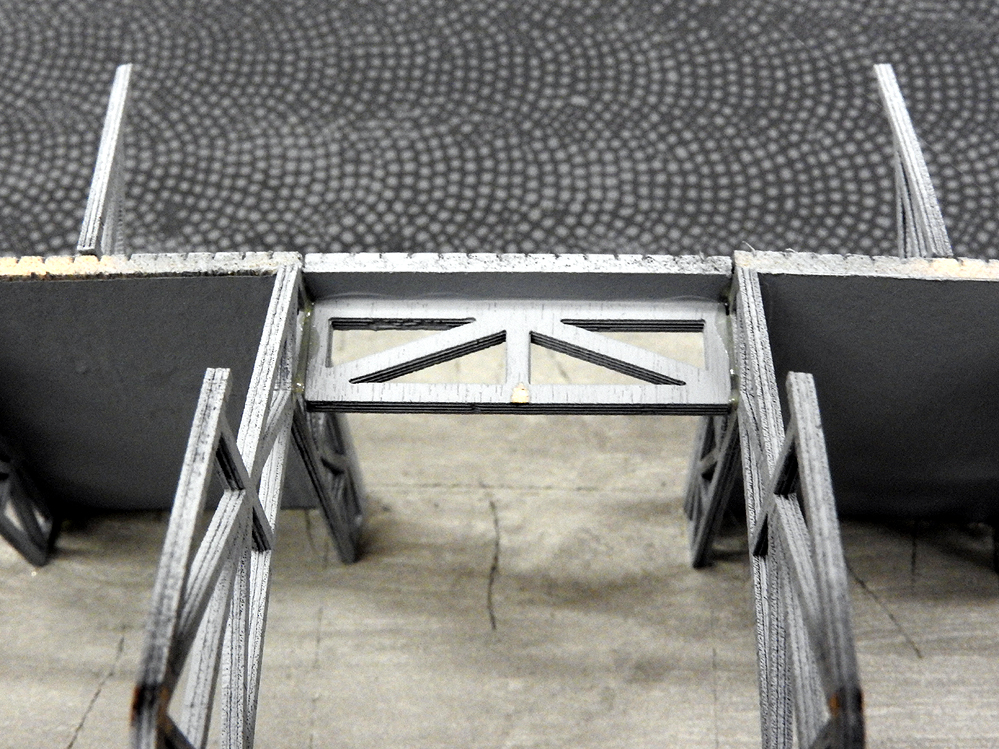
Nun mussten noch die Laufschienen für die Rolltore angebracht werden. Eine kleine Lehre aus einem Abfallstück sorgt für die richtige Höhe. Die Schienen sind gelaserte Laser-Kartonstreifen (0,9 mm dick) Das Lasern hat hier den Vorteil, dass die schmalen Streifen korrekt gerade sind. Beim Schneiden mit einem Messer würden sie sich sämtlich bogenförmig von der Klinge hinwegwinden. Ob sie auch so schön wieder in die Gerade gezwirbelt werden können? So ist es einfacher.
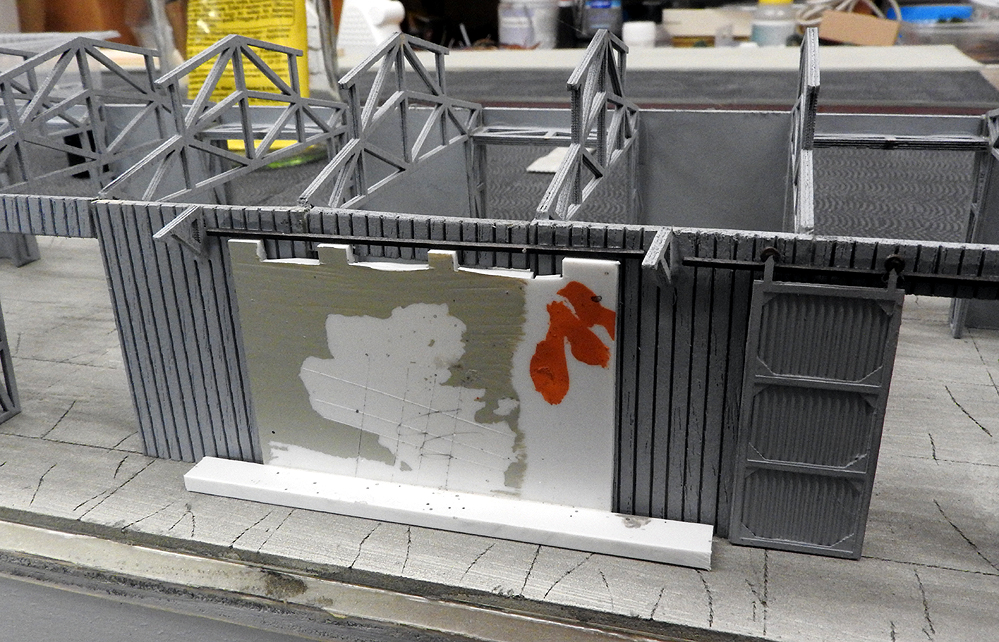
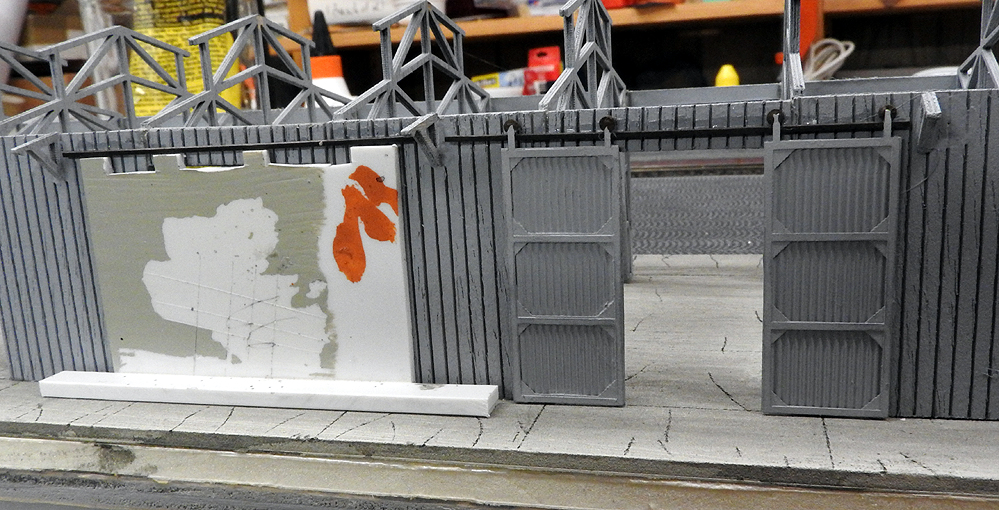
In den langen Wintertagen habe ich die Rohbauten aus dem Kibribahnhof „Calw“ weiter vervollständigt. Die den Bausätzen beigelegten „Gardinen“ passen nun gar nicht zu einem spartanischen Verwaltungsgebäude. Hier habe ich die Fenstergardinen lediglich mit einem Flachpinsel und Acrylfarbe angelegt und danach mit einem dunklen „Raumgrau“ hinterlegt. Gefällt mir ganz gut so, lediglich die Fenstergardinen hätten ein wenig mehr in Richtung „Nikotingelb“ tendieren können. Nun ja, im nächsten Leben . . . .

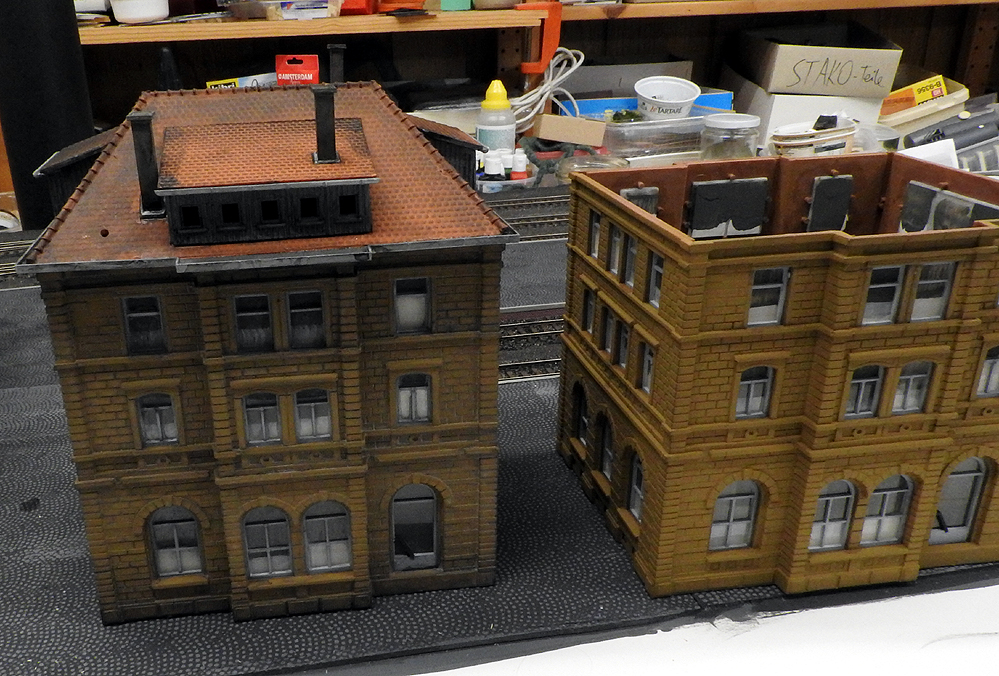
Da der Fischereihafen nicht in der direkten Nachbarschaft eines rußspeienden Industriegebiets sondern eher an salziger Nordseeluft liegt, habe ich die Patinierung zurückhaltend im wesentlichen mit grau vorgenommen, nur die roten Dächer haben Rußablagerungen von der Kohlenheizung.
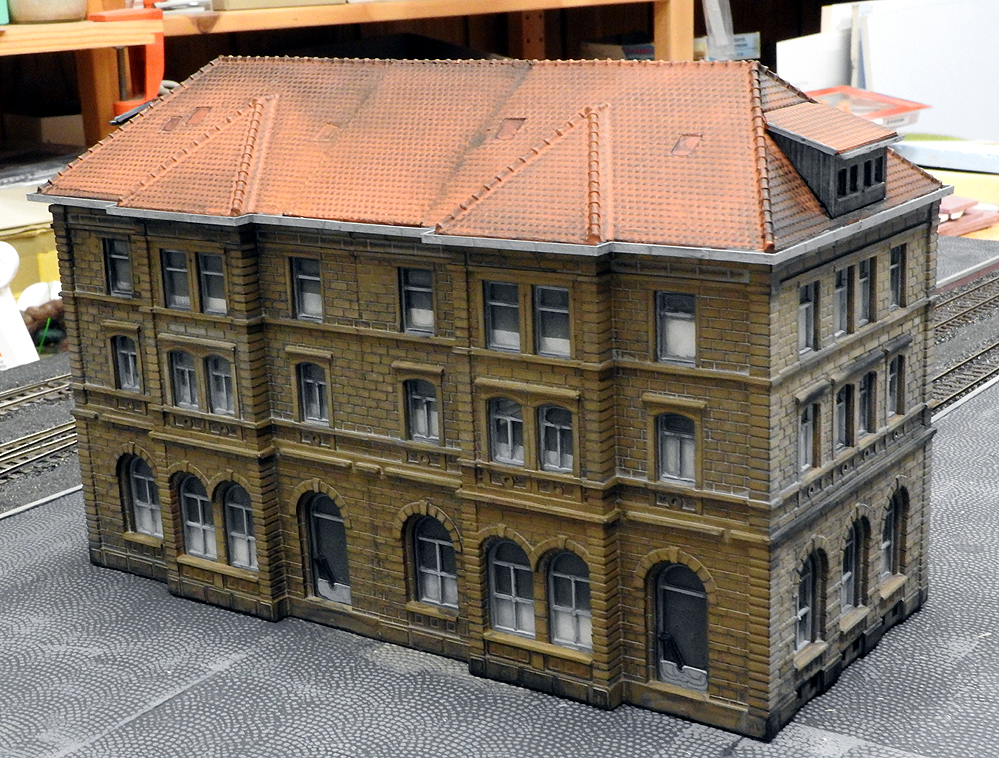
Das Gebäude steht zur Zeit "nur so" drauf. Die Dachmöblierung ist mittlerweile auch drauf, habe nur kein aktuelles Foto davon. Na ja, . .
So, das wäre die "Wasserstandsmeldung" für den heutigen Tag. Wenn´s mal wieder etwas zu zeigen gibt, werdet ihr es hier zu sehen bekommen. Versprochen!
Schaunmermal, dann seh´n wir weiter!